Frequently Asked Questions
A list of frequently asked questions if given on the left, if you cannot find
you're question here, please do not hesitate to contact the
nearest dealer.
WHY ARE PARAMOTOR WINGS CERTIFIED FOR FREE FLYING?
The certification in Europe (CEN) exists only for free flying gliders and there is no actual certification for paramotor configuration of the wing - so all industry continues to certify paramotor wings for free flying (accordingly typical S size wing is certified for 65kg to 85kg only) and then just by making additional load test for maximum weight, including paramotor 100 kg - 165 kg confirming it for PPG use.
This is the policy we at APCO follow too.
HOW IS A PARAGLIDER CONSTRUCTED AT APCO?
A paraglider is constructed from a top and bottom surface connected by ribs.
One top and bottom panel, together with the connecting ribs is called a cell.
In some
models,
secondary ribs are of a diagonal design and sewn between the main ribs.
Each cell has an opening on the lower front part. The cells fill with air under
pressure forcing the panels to take the shape dictated by the air-foil section
of the ribs.
It is APCO's philosophy to have
one person try to
complete a unit, including all vital stages from start to
finish. Your glider is therefore cut as a set and sewn as a set,
and the line set on your glider has been individually cut and sewn as a set.
WHY IS IT WRITTEN IN APCO's REFLEX WINGS (Force, Force SP,
Lift, Lift EZ...) MANUALS "Big Ears is unavailable"?
Due to the behavior of reflex profile, it is very difficult and sometimes even not possible to create a deflation by pulling on the A riser, therefore it is nearly impossible and uncomfortable to perform Big Ears maneuver on reflex wings.
WHY DOES APCO CHANGE ASPECT RATIO
FOR DIFFERENT SIZES OF SAME WING MODEL?
Why does APCO change aspect ratio for different sizes of same wing model?
(Contrary to the mainstream manufacturers who use zooming/scaling, keeping aspect ratio constant)
Indeed it does sound odd.
Why should APCO insist on sizing system which is not popular with other manufacturers?
Let's see - to every problem there is always more than one solution and probably you can reach the goal either way.
The question is what is more efficient and offers better optimization.
A.R.O. by APCO represents a design philosophy which we believe brings the best results possible to the subject of sizing wings for paragliding/paramotoring
Contrary to most companies that scale/zoom their models up and down to create different sizes, we at Apco believe this is not always the optimal way,
so for different sizes we build in different aspect ratio
When APCO designs different sizes of wings, we change the area, span and also aspect ratio
The span of the wing and size are changed by adding or deducting the amount of panels (wing segments). This is In order to not only change the area of the wing, but also the Aspect Ratio (A.R)!
This way we reach a better result as the change in A.R compensates for many other variables.
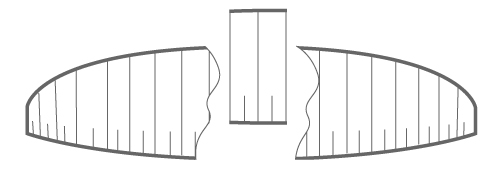
Our experience proves that even though traditional scaling (zooming) seems to be logical, easy to understand, it does not automatically produce the best results when changing the size of the wing. Indeed when using scaling the aspect ratio is preserved and kept constant, but many other parameters are not scaled correctly or not scaled at all:
1. The drag produced by pilot stays about the same through all sizes.
2. The diameter of the lines are not scaled, therefore the drag is unchanged as well as elasticity of the lines
3. The cloth thickens and the surface drag is not changed
4. Reynolds numbers are not scaled As the Air's density and Viscosity stay unchanged.
5.And so on...
As a result when zooming, many times manufacturers have difficulties repeating handling and safety of the wing in all sizes!
It is well known that small sizes when zoomed behave more aggressively, leading to certification difficulties in the same class.
Therefore smaller wing sizes designed by APCO with lower aspect ratio and larger sizes allow to build in higher aspect which can improve performance where possible without being aggressive.
To be systematic, we at APCO on most of the wings during R&D evaluate both approaches (classic zooming and A.R.O.) and judge the final, practical result, choosing the best.
In case, as happened with Karma EVO, we achieved better result by traditional zooming - which is why we launched a glider which is zoomed and maintains same aspect ratio between S and M sizes. We did finish the design and successfully certified the Karma EVO in S and M sizes for both versions - (zoomed, with constant Aspect Ratio and APCO's A.R.O. applied) . In the end we chose the better one - in this case the zoomed version.
In the same way when you have a wing which in our opinion gives an optimal result by using our A.R.O. system - then that is the system we use and that is the case with most of our gliders.
Also on very high aspect ratio wings - e.g. Enigma or Zefira we favor traditional approach by zooming, maintaining the same aspect ratio on each size, as on high aspect ratio wings the difference in span is too big between different sizes if we change the size by changing the span.
As you can see, we are choosing the best sizing system for each particular wing design be it A.R.O. or classic zooming.
We hope this explanation helps to explain the reason behind our approach.
HOW SHOULD BRAKES ON APCO GLIDERS BE ADJUSTED?
The line should be adjusted with not less than 10 cm of movement before activation of the
brake when the paraglider is inflated above your head. The trailing edge should not pull
down when in a state of hands off.
An additional brake line has been installed on a few models to activate the stabilizer for improved handling.
The brake line should be adjusted in a way that the stabilizer is activated after 60-100 mm.
of free movement of the main brake line. Caution should be taken when the main brake line is adjusted,
so that the line activating the stabilizer is readjusted, in order to maintain the same free movement of the
brake before the stabilizer is activated
HOW SHOULD LINES BE MAINTAINED AND OR REPLACED?
Super-aramid lines are known to be sensitive to the influence of the elements.
They must be carefully inspected periodically. The pilots, in their own interest, must observe the
following points to ensure maximum performance and safety from the glider.
- Avoid sharp bending and squeezing of the lines
- Do not step on the lines
- Take care of your lines in crowded take off areas
- Do not pull on the lines if they get caught on rocks or vegetation
- Avoid getting the lines wet. Dry them as soon as possible at room temperature if they do
IT IS STRICTLY RECOMMENDED TO CHANGE THE BOTTOM LINES ON EVERY PARAGLIDER ONCE A YEAR OR EVERY 100 HOURS, WHICH EVER COMES FIRST. THE REST OF THE LINES MUST BE CHECKED YEARLY AND REPLACED IF NECESSARY. THIS RECOMMENDATION IS IN LINE WITH ISRAELI REGULATIONS, BINDING IN ISRAEL. AS AN ALTERNATIVE, WE SUGGEST FOR YOU TO FOLLOW THE REGULATIONS SET BY YOUR NATIONAL AUTHORITIES WITH REGARD TO LINE MAINTENANCE AND REPLACEMENT.
NEVER REPLACE THE LINES WITH DIFFERENT DIAMETER OR TYPE OF LINES AS ALL GLIDERS WERE LOAD TESTED FOR SAFETY IN THEIR ORIGINAL CONFIGURATION. CHANGING LINE DIAMETER/STRENGTHS CAN HAVE FATAL CONSEQUENCES.
WHAT ARE THE HOLES IN THE TOP OF SOME MODELS OF APCO GLIDERS?
The diagonal ribs used in the newer gliders made by APCO
are stitched to the center of the panels of the top surface.
Unlike other ribs, the position to stitch these ribs has to be marked, which is done by
punching small holes in the correct position.The small holes do not influence the gliders
performance and are not mistakes, but necessary for the accurate manufacture of the glider.
IN WHAT COLORS CAN APCO GLIDERS BE ORDERD?
Each model has a standard color pattern, and a standard range of colors.
We prefer to stick to these patterns and colors to improve product identity,
but custom colors are available, at an increased cost. It is also possible to put logos on the gliders,
specifically for sponsored gliders.
Contact your
dealer
for more information and quotes.
HOW DO I MAKE A CUSTOM COLOR OR LOGO ORDER?
To place a order for a custom color or a glider with a logo on it, or both, you will have to
provide your dealer with the following information:
- Model of Glider
- Size of Glider
- Standard or custom color
- If custom, include exact details, with a diagram if possible
- Siliconized or non siliconized cloth†
- APCO logo on under surface?
- APCO logos on wing tips?
- Insignia/Logo‡
†If you are intending to place a logo or any insignia on the glider yourself,
it is nessesarry to order the glider with a non-siliconized bottom surface,
since insignia cloth does not stick to the standard siliconized cloth. It is possible to buy the
Insignia cloth from APCO through your dealer.
If the glider surfaces, as a result of customer request, are produced from cloth different to
standard cloth with which glider was certified. The glider no longer meets the formal certification requirements.
‡Include a exact diagram of what the glider should look like with the logo on it.
Also include a high quality copy of the logo. The insignia cloth used for making logos are available in
many colors, but not fading from one color to another i.e. in plain colors only. Also keep in mind that a
very large amount of insignia added to a glider makes it heavy, and it becomes harder to launch. It may be
necessary to construct the logo in part, into the glider using the glider fabric.
WHAT IS MEANT BY "HOOK IN", "ALL UP" AND "PILOT" WEIGHT?
The three different terms used to describe pilot weight have led to some misunderstanding. During certification,
"all up weight" is quoted, which is the total weight of the pilot and all equipment, including the glider.
This is the correct weight to use when calculating wing loading. At APCO we have always used "hook in" weight,
to refer to what our gliders are designed to carry. It therefore excludes the weight of the glider.
The technical information about all our gliders refers specifically to hook in weight. "Pilot weight"
is a potentially confusing term, and is not used by APCO.
Recently however, we have changed our policy in favor of the industry norm of "all up weight".
The ranges quoted for the Bagheera, Allegra and later models are "all up". This is in order to
avoid misunderstanding in the flying community. All the gliders before Bagheera and Allegra have been
quoted for "hook in" weight (total weight, excluding the weight of the glider).
All our future gliders, including Bagheera and Allegra, will be quoted for "all up" weight
(total weight incl. the weight of the glider).
WHAT IS APCO'S POLICY W.R.T FITTING OF TRIMMERS?
Our gliders are usually not certified with trimmers, except for the Keara and tandem gliders.
However, in certain special situations we are willing to provide trimmers, with the understanding
that the glider is then not certified.
WHAT MATERIALS ARE USED AT APCO?
The glider is made from high tear resistant Rip stop Nylon cloth, which is P.U.
coated to zero porosity and siliconized to make the fabric greatly resistant to the elements.
The cloth for the top and bottom panels, and the ribs is of different types due to their different functions.
The lines are made of Super-aramid covered with a polyester sheath for
protection against wear and abrasion. The bottom section of the brake lines is made of
Polyester because of its better mechanical properties to resist the bending around
the steel ring of the brake line guide.
The carabiners that attach the lines to the v-lines are made of high corrosion resistant stainless steel
WHY IS A SPECIFIC CLOTH USED
This has lately become a hot issue especially on some markets, therefore we would like to share our experience and
opinion on this matter with you: Due to APCO's use of superior paragliding cloth and our 3 year/250 hour
warranty, some manufacturers felt threatened and believed that APCO has been taking
too big a slice of their market share. (I wish that this was the case and all that was required to
increase the market share was to improve the quality of the cloth! It takes a lot more than putting some
silicon on the cloth. The product has to offer competitive safety, performance, service and price.)
The manufacturers searched for a new method of increasing their sales by attacking APCO through some
magazines and other publications, publishing recently a number of articles claiming that "porosity is
unimportant and that it is actually better to use "porous cloth". We view this as a naive attempt to
convince "uninformed" customers that "Black is White".
The facts are as follows: We have been using this cloth since 1992, and during these years we have not
received a single claim about deteriorating performance as a result of loss of porosity of the cloth.
Actually, until today, we weren't required to pay a single penny to unsatisfied customers within the
frame of our warranty. Please check with our competitors how many times they have had to battle with a
customer because the glider did not launch or stalled due to porosity problems.
We have made a comprehensive study, comparing cloth quality. The results are that the porosity of our
new cloth is 2-3 times better and the tearing resistance is 10%-15% better than cloth used by our
competitors. After 500 hours of use, the porosity of our cloth will be 10 times better and the
tearing resistance will be 7 times stronger.
Hours Used |
Porosity: JDC-Porosity Meter |
Tearing Resistance |
|
APCO |
Competition |
APCO |
Competition |
New |
800-1000 sec |
300-500 sec |
4.5 kg |
4.0 kg |
500 |
200-250 sec |
20-25 sec |
3.5 kg |
0.5 kg |
These results have been proven a number of times and are easy to display. On every APCO paraglider there is a
small section of non-siliconized cloth where the logo is applied (the rest is siliconized).
Since there are 2 different types of cloth on the same glider, undergoing the same atmospheric
conditions and exposure to the elements for the same amount of time, it makes the experiment
precise and gives reliable comparative data. We often have used gliders here and have obtained
the same results, showing the advantages of silicon coating on paragliding cloth.
Another typical argument we often face is that the porosity is good, but the cloth is bad due to
too much elasticity. Again this is untrue and we do not wish to argue as to what is better for the
glider - elastic or rigid cloth - we leave that up to you. However, what matters to the customer is
whether our product flies as well as or better than our competitors product, even after 200-400 hours of
flying. If you find that the performance of our used products deteriorated the same or less than the
performance of our competitors product, the inevitable conclusion must be that the claim of
elasticity of fabric is bad for our products is untrue and speculative. Much additional ink
could be wasted over this particular subject, but I believe that your own experience will
coincide with our findings. We often receive phone calls from our dealers thankfully noting
that school gliders previously used in their schools had to be thrown out after one year.
Now that they are using APCO Prima with silicon cloth, the glider is still as good as
new even in its second or third year. Also have a look at the
Pilot's Comments
WHY IS PERFORMANCE DATA, AS BEST L/D, NOT PUBLISHED?
In our opinion, some of the aerodynamical performance data frequently published lacks reliability
and is somewhat inflationary. Some aerodynamical parameters like L/D, polar etc.
are difficult to measure scientifically with small enough error margins without the use of
very expensive and complicated equipment (not usually available): full size wind tunnels in
which the paraglider could be tested and/or proper simulation theory. Outdoor testing based
on vario and speed meter may have too big an error margin, due to the large number of changing
parameters which are not taken into consideration and the optimistic approach of interested
parties when they publicize the results of the tests and often demonstrate a selective
approach in an effort to prove the superiority of one product compared to the next.
We have never publicized the results of our L/D tests as we wished to refrain from entering
into this inflationary race.
GATE LOCK CARABINER CERTIFICATION
Dear Friends,
Recently there has been a lot of confusion regarding airworthiness of paragliding
carabiners from Austrian Alpin.
We offer carabiners which resemble the carabiners from
Austrian Alpin in their shape. We would like to reassure all of you that our carabiners
are free of any fault and are perfectly airworthy.
Our carabiners have very precise tolerance between the gate and the catch, preventing periodical bending cycles under repeated loads. So no loss of strength is recorded after prolonged use. The carabiner is made from aircraft quality 7075 Aluminium Alloy Hot Forged and individually tested. This is a manufacturing technique guaranteeing the best strength results (as the material is free of internal stress).
The carabiners from most other manufacturers are made by bending aluminium rod which introduces internal tension and invisible micro cracks – significantly reducing the strength of the carabiner during its lifespan, accelerated by the periodical bending cycles under repeated load due to the big tolerance between the gate and the body catch.
To reconfirm our data, we asked the Israel Institute of Standards
to test the breaking strength of carabiner both before and after repeated bending cycle.
Test results received from them, showing carabiner before bending carries
2.5 ton and after prolonged use is still good for at least 1,700-1,800 kg.
A copy of the test results is available for
download here.
NRG XC II Vs. NRG PRO II
|
NRG XC II |
NRG PRO II |
Description |
Cross Country wing - easy to handle, take-off and land.
- Fast and agile at trim speed.
- Stable and more relaxed in any accelerated flight mode (trimmers or speed bar)
|
Slalom racing wing – extremely manueverable and responsive wing. Designed to allow the fastest possible transition between trim speed to fully acclerated and back to trim speed. Highly defined and pronounced reflex profile for safety in extreme flying. |
Aimed at |
Experienced pilots, looking for a thrilling cross country wing which delivers more speed and andrenalin than the average xc wing. |
Very experienced pilots/professionals who can handle its responsiveness to the lightest of input.
Pilots looking for the ultimate paramotor wing for slalom racing/ACRO flying/adrenalin. |
Build differences |
Fully sheathed lines for easy handling and durability |
Unsheathed competition lines for maximum performance. |
Unique Features |
ABS - Automatic Balance System |
✔ - improved stabillity in accelerated flight |
✘ - Removed for the highest agility at any flight speed |
SRS – Stall Resistance System |
✔ - Easier launch and safety due to stall resistance |
✘ - Removed for quicker transition from trim speed to accelerated and back to trim speed |
Tip Steering handles |
✔ - Optional for ease of use in XC flights |
✘ - Removed for use with 2D system only for maximum agility and wing control |
2D Steering |
✔ |
✔ |
WSS - Wind Scoop System |
✔ |
✔ |
EHP - Embedded hook in point |
✔ |
✔ |
OAA – One Action Acceleration |
✔ |
✔ |
HIT Valves |
✔ |
✔ |
Flexon battens |
✔ |
✔ |
Ball bearing pulleys |
✔ |
✔ |